Zero-waste manufacturing is a transformative approach that aims to eliminate waste through efficient resource use and sustainable practices. It prioritizes the waste hierarchy, encouraging prevention, reduction, reuse, and recycling. By implementing innovative strategies and collaborating with suppliers, companies can improve efficiency and minimize environmental impact. Evaluating waste levels and engaging employees in sustainability initiatives are likewise essential. By adopting these principles, manufacturers can contribute to a circular economy and promote environmental stewardship. There's much more to explore on this topic.
Article Highlights
- Adopt the waste hierarchy: prioritize prevention, reduction, reuse, and recycling to minimize waste in production processes.
- Implement sustainable design practices that facilitate easy recycling or repurposing of products.
- Conduct regular waste audits and analyze data to track efficiency and identify areas for improvement.
- Collaborate with suppliers to optimize material usage and reduce excess inventory, enhancing resource efficiency.
- Explore innovative strategies like closed-loop systems and material recovery to continuously recycle and reuse materials.
Understanding Zero-Waste Manufacturing
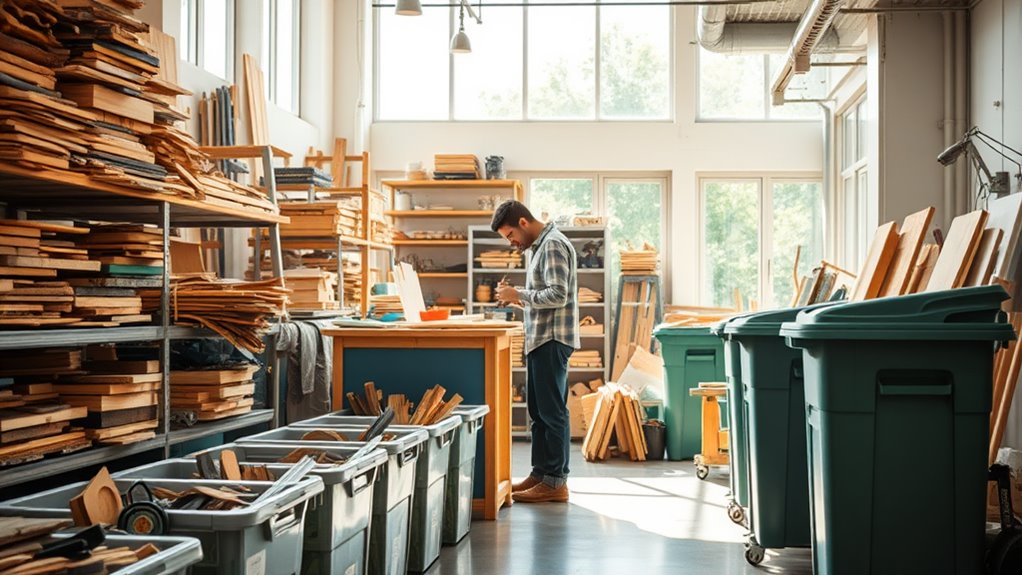
Zero-waste manufacturing embodies a transformative approach to production that seeks to eliminate waste entirely. It redefines traditional production methods by prioritizing the waste hierarchy, which emphasizes reducing waste at the source, reusing materials, and recycling what remains. This method encourages companies to rethink their processes and find innovative ways to minimize their environmental impact. Sustainable sourcing plays an essential role in this approach, as it involves selecting materials that are renewable, responsibly harvested, and produced with minimal ecological footprints. By integrating sustainable sourcing practices, manufacturers not only improve their resource efficiency but also contribute to a circular economy. In the end, zero-waste manufacturing aims to create a system where every material is utilized, reducing the burden on landfills and promoting environmental sustainability.
The Principles of Zero-Waste Production
At the heart of zero-waste manufacturing are key principles that guide production processes toward sustainability. Central to these principles is the waste hierarchy, which prioritizes waste prevention, reduction, reuse, and recycling. By following this hierarchy, manufacturers can minimize waste at every stage of production. Sustainable design plays an essential role, as it encourages the creation of products that are easy to recycle or repurpose, reducing the overall environmental impact. Implementing these principles helps companies not only decrease their waste output but also enhance efficiency and reduce costs. As industries adopt zero-waste practices, they contribute to a circular economy, promoting innovation and supporting environmental stewardship as they meet consumer demand for sustainable products.
Assessing Your Current Waste Levels
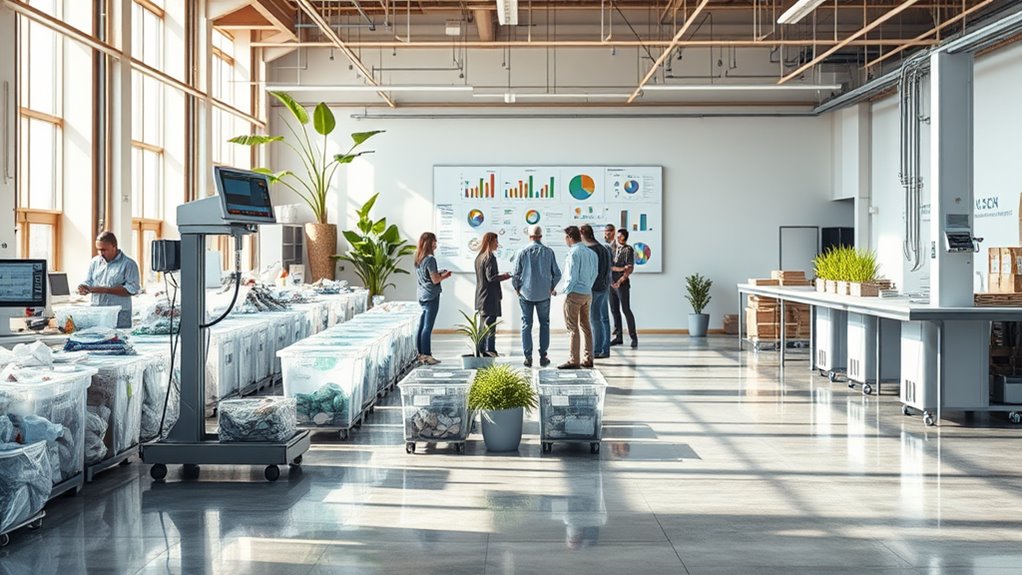
How can manufacturers effectively gauge their waste output? A thorough waste audit is vital. By collecting data through waste categorization, companies can identify specific waste streams and their environmental impact. This process often involves data analysis to track production metrics against efficiency benchmarks. Employee feedback can provide valuable insights, revealing areas for improvement. Furthermore, resource mapping helps visualize how materials flow through the production process, highlighting inefficiencies. Collaborating with suppliers can also improve sustainability goals by ensuring responsible sourcing and reducing waste upstream. Comprehending current waste levels is critical for setting actionable targets and nurturing a culture of continuous improvement in zero-waste manufacturing.
Strategies for Waste Reduction
In the pursuit of zero-waste manufacturing, companies can implement various strategies for waste reduction. Efficient material utilization, recycling and reusing techniques, and process optimization methods are key components in minimizing waste. By adopting these approaches, manufacturers can considerably improve their sustainability efforts.
Efficient Material Utilization
Although many manufacturers aim for efficiency, achieving effective material utilization remains a critical challenge in waste reduction. To improve material efficiency and promote resource optimization, organizations can implement several key strategies:
- Design for Manufacturability: Simplifying designs can minimize material waste during production.
- Process Improvement: Regularly evaluating and refining manufacturing processes can lead to better resource use.
- Supplier Collaboration: Working closely with suppliers can guarantee materials are delivered in ideal quantities, reducing excess.
Recycling and Reusing Techniques
Recycling and reusing techniques are essential components of a zero-waste manufacturing strategy. These methods not just minimize waste but additionally promote sustainability. One effective approach is integrating composting techniques, which involve breaking down organic materials into nutrient-rich compost, thereby reducing landfill contributions. Manufacturers can likewise adopt upcycling practices, where discarded materials are transformed into new products of higher value. For instance, scrap metal can be turned into unique art pieces or functional furniture. By implementing these strategies, businesses not only conserve resources but also reduce their environmental impact. In the end, embracing recycling and reusing techniques cultivates a culture of sustainability, encouraging innovation and creativity as well as contributing to a healthier planet.
Process Optimization Methods
Integrating recycling and reusing techniques lays a solid foundation for further advancements in waste reduction. Effective process optimization methods improve resource allocation and streamline process flow, minimizing waste throughout manufacturing.
Key strategies include:
- Lean Manufacturing: Focuses on eliminating non-value-added activities, improving efficiency.
- Six Sigma: Uses data-driven approaches to reduce defects and variation in processes.
- Just-In-Time (JIT): Aligns production schedules with demand, reducing inventory waste.
Implementing Circular Economy Practices
As businesses endeavor to minimize waste, implementing circular economy practices has become essential for sustainable manufacturing. These practices prioritize circular design and resource efficiency, allowing companies to reduce their environmental impact during maximizing their output. By focusing on the entire lifecycle of products, manufacturers can create systems that not only lessen waste but also promote the reuse and recycling of materials.
Circular Economy Practices | Benefits |
---|---|
Material Recovery | Reduces landfill waste |
Product Lifecycle Extension | Increases product value |
Design for Disassembly | Facilitates recycling |
Resource Sharing | Optimizes usage |
Sustainable Sourcing | Lowers environmental impact |
Through these strategies, businesses can make a shift towards a more resilient and responsible manufacturing model.
Innovations in Sustainable Materials
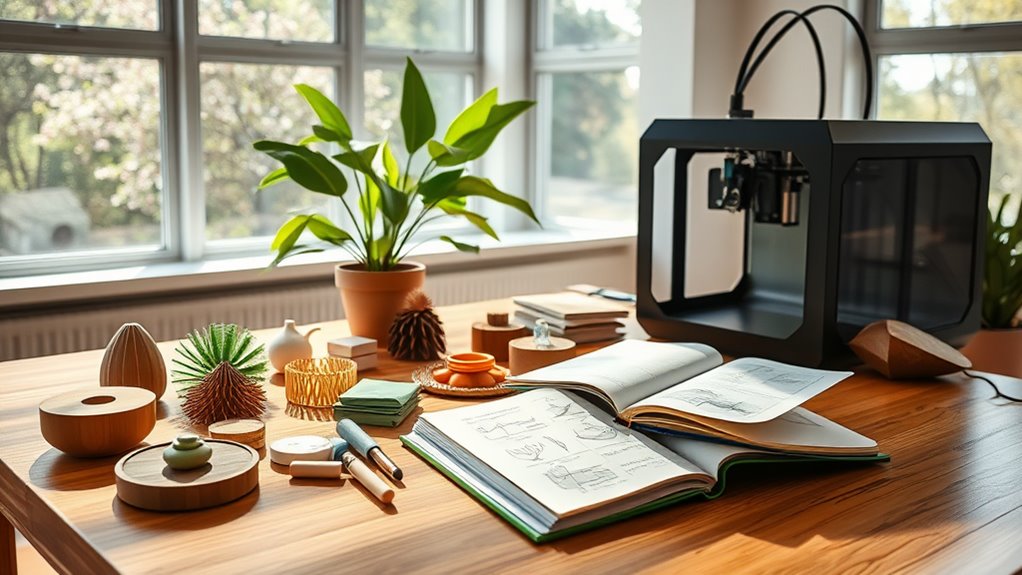
The shift in the direction of a circular economy sets the stage for innovations in sustainable materials that can further improve manufacturing practices. Companies are increasingly adopting materials that minimize environmental impact, like biodegradable composites and recycled plastics. These advancements not only reduce waste but as well help in conserving resources.
Key innovations include:
- Biodegradable Composites: Made from natural fibers, these materials decompose easily, leaving no harmful residues.
- Recycled Plastics: Utilizing post-consumer plastics reduces the need for virgin materials, cutting down on energy and resource consumption.
- Bio-based Materials: Sourced from renewable resources, these alternatives provide a sustainable option without compromising on performance.
Such innovations pave the way for a more sustainable future in manufacturing, aligning with zero-waste objectives.
Employee Engagement and Training
Employee engagement and training play a crucial role in cultivating a culture of sustainability within manufacturing. By implementing effective training programs, companies can boost employee motivation and promote sustainable practices. Encouraging team collaboration nurtures a sense of ownership and accountability, whereas waste awareness initiatives help employees understand their impact. Continuous improvement is critical, and leadership involvement guarantees that sustainability goals align with the company's vision. Gathering employee feedback helps identify areas for skill development, making the workforce more adept at implementing eco-friendly strategies. This cultural change not only improves operational efficiency but also creates a more committed workforce, ultimately driving the success of zero-waste initiatives and contributing to a healthier environment.
Measuring Success in Zero-Waste Initiatives
Measuring success in zero-waste initiatives requires a clear framework that assesses not merely the volume of waste diverted from landfills but also the overall impact on operational practices. Effective measurement incorporates various success metrics and performance indicators, ensuring alignment with sustainability goals.
Key components include:
- Quantitative analysis of waste benchmarks and diversion rates
- Qualitative measures such as stakeholder feedback and employee engagement
- Impact assessments that evaluate changes in operational efficiency
Case Studies of Successful Zero-Waste Manufacturers
Many manufacturers are leading the way in zero-waste practices by implementing innovative material reuse strategies and closed-loop production systems. These case studies highlight how companies transform waste into valuable products, showcasing the potential for sustainability in manufacturing. By examining these successful examples, it's clear that a shift in the direction of zero-waste is both achievable and beneficial.
Innovative Material Reuse Strategies
As businesses increasingly recognize the importance of sustainability, innovative material reuse strategies have emerged as essential components of zero-waste manufacturing. These strategies focus on maximizing resource efficiency through various methods, including:
- Material exchange programs that facilitate surplus utilization among manufacturers.
- Design collaboration to guarantee products are created for easy disassembly and upcycling innovations.
- Community partnerships that promote resource sharing and industrial symbiosis.
Closed-Loop Production Systems
Even though implementing closed-loop production systems can seem intimidating, numerous manufacturers have successfully adopted these models, setting benchmarks for zero-waste practices. These companies utilize closed loop design to guarantee that materials are continuously recycled and reused within their operations. For example, a leading textile manufacturer has transformed waste fibers into new fabrics, showcasing effective resource recovery. Another case features a furniture maker that repurposes wood scraps into high-quality products, minimizing landfill contributions. By focusing on efficiency and sustainability, these manufacturers not just reduce waste but also improve their bottom lines. Their achievements highlight the potential of closed-loop systems to create a circular economy, inspiring others to follow suit in their quest toward zero waste. This approach extends beyond industrial settings, influencing consumer trends such as white linen bedroom styling, where sustainable textiles are favored for their durability and minimal environmental impact. As demand for eco-friendly products rises, businesses that embrace closed-loop production gain a competitive edge by aligning with conscientious consumers. Ultimately, these efforts contribute to a more resilient and responsible global economy.
Waste-to-Product Transformations
Although the expedition to zero-waste manufacturing can be complex, several companies have turned their waste into valuable products, demonstrating innovative approaches that others can emulate. These successful manufacturers utilize waste valorization techniques and byproduct utilization methods to create sustainable solutions.
Key examples include:
- Coffee grounds repurposed into biodegradable packaging: A coffee company transformed their waste into a sustainable product, reducing landfill contributions.
- Textile scraps converted into insulation material: A clothing manufacturer creatively used leftover fabric, contributing to eco-friendly construction.
- Food waste transformed into energy: A food processor harnessed organic waste to produce biogas, energizing their facility and minimizing environmental impact.
These case studies highlight the potential for businesses to innovate as they effectively reduce waste.
Future Trends in Zero-Waste Manufacturing
With the increasing urgency to combat climate change and resource depletion, zero-waste manufacturing is poised to evolve considerably in the coming years. Sustainable technology will play a key role, enabling businesses to adopt eco-friendly innovations as they meet consumer demand for greener products. Industry collaboration will strengthen circular supply chains, making waste reduction a shared goal. Regulatory changes are likely to drive companies toward green certifications, enhancing their competitive advantage. As digital transformation progresses, lifecycle analysis tools will help firms track resource use and waste more effectively. In the end, these trends will not just support a sustainable future but will redefine manufacturing paradigms, ensuring that businesses thrive in a world that's increasingly focused on zero waste.
Frequently Asked Questions
How Can Small Businesses Adopt Zero-Waste Manufacturing Practices?
Small businesses can adopt zero-waste manufacturing practices by implementing waste reduction strategies that minimize material use and encourage recycling. They should focus on sustainable sourcing, selecting materials that are eco-friendly and recyclable. Collaborating with suppliers who share similar values can improve these efforts. By regularly evaluating their processes, small businesses can identify areas for improvement, eventually leading to reduced waste and a positive impact on the environment as they maintain efficiency and profitability.
What Certifications Are Available for Zero-Waste Manufacturing?
In a world where sustainability's the new gold standard, businesses seek recognition through certifications that validate their eco-friendly efforts. Various certification types exist for zero-waste manufacturing, such as ISO 14001, which focuses on environmental management systems, and Cradle to Cradle, emphasizing circular design. These industry standards not merely boost credibility but additionally guide organizations toward sustainable practices, ensuring they meet both consumer expectations and regulatory demands in today's conscientious market.
How Do Regulations Impact Zero-Waste Manufacturing Efforts?
Regulations greatly influence zero-waste manufacturing efforts, presenting various regulatory challenges. Companies often find themselves maneuvering through complex laws that can hinder their initiatives. To overcome these obstacles, they develop compliance strategies that align with both sustainability goals and legal requirements. By doing so, they can guarantee their operations remain environmentally friendly during compliance with regulations. These strategies not just improve efficiency but additionally cultivate a culture of responsibility within the organization.
What Are the Financial Benefits of Zero-Waste Manufacturing?
In the realm of manufacturing, the allure of zero-waste practices shines like a beacon. For companies, embracing this approach can reveal significant cost savings, as waste reduction leads to lower disposal fees and resource efficiency. Furthermore, the investment returns can be substantial, as consumers increasingly favor sustainable brands. By weaving sustainability into their operations, businesses not just improve their reputation but likewise pave the way for long-term financial prosperity.
Can Zero-Waste Principles Apply to Service Industries as Well?
The question of whether zero-waste principles can apply to service industries is intriguing. Many experts believe they can, as service sustainability often hinges on efficient resource use and waste reduction. For instance, businesses can minimize paper usage, implement digital solutions, and streamline processes to cut down on waste. By embracing these principles, service industries not solely improve their environmental impact but additionally boost their efficiency and potentially lower operational costs, benefiting both the business and the planet.